Unique fabricating chapter 7 – Chapter 7 of our journey unveils the unique fabricating methods that set this chapter apart. From innovative techniques to carefully selected materials and meticulous design considerations, we delve into the intricacies that make Chapter 7 truly exceptional.
As we explore the fabricating methods, we’ll uncover the advantages and limitations of each approach, gaining insights into the complexities of material properties and selection. The interplay between design and fabrication will be brought to light, showcasing how innovative design approaches can push the boundaries of possibility.
Fabricating Methods
In Chapter 7, we delve into the extraordinary fabricating methods that set this chapter apart. These techniques and processes push the boundaries of traditional fabrication, enabling the creation of intricate and innovative designs.
Additive Manufacturing
Additive manufacturing, also known as 3D printing, is a transformative technology that has revolutionized the fabrication industry. This method involves building a three-dimensional object by depositing material layer by layer, allowing for complex geometries and intricate details that are difficult to achieve through conventional methods.
Unique fabricating chapter 7 reveals the secrets of masterful craftsmanship. Take a detour to wind breaker chapter 443 for a glimpse of the intricate weaving techniques that create timeless garments. Returning to unique fabricating chapter 7, you’ll appreciate the depth of knowledge and skill that goes into every stitch.
Advantages:
- Unprecedented design freedom and flexibility
- Production of prototypes and small batches with minimal tooling
- Reduced material waste and increased efficiency
Limitations:
- Limited material selection and mechanical properties
- Can be time-consuming for large-scale production
- Post-processing requirements, such as support removal and finishing
Subtractive Manufacturing
Subtractive manufacturing, often referred to as machining, is a traditional fabrication method that involves removing material from a solid block to create the desired shape. This includes processes such as milling, turning, and drilling.
Advantages:
- High precision and accuracy
- Wide range of materials and finishes
- Suitable for mass production
Limitations:
- Material waste during the cutting process
- Can be labor-intensive and time-consuming
- Requires specialized machinery and skilled operators
Hybrid Fabrication, Unique fabricating chapter 7
Hybrid fabrication combines additive and subtractive methods to create complex and high-performance parts. This approach utilizes the advantages of both techniques, enabling the production of intricate geometries and precise features.
Advantages:
- Greater design freedom and complexity
- Improved material properties and durability
- Reduced production time and costs
Limitations:
- Can be more complex and require specialized equipment
- May involve trade-offs between different fabrication methods
- Requires careful planning and coordination
Material Properties and Selection
The fabrication processes in Chapter 7 demand unique material properties to achieve the desired functionalities and performance. The selection of appropriate materials is critical to ensure successful fabrication and optimal device performance.
The material properties required for Chapter 7 fabrications include high electrical conductivity, thermal stability, mechanical strength, and chemical inertness. These properties are essential for ensuring efficient current flow, maintaining structural integrity under various operating conditions, and preventing degradation or contamination of the fabricated devices.
The world of unique fabricating is ever-evolving, and chapter 7 is no exception. With its intricate details and captivating plot, this chapter has left readers on the edge of their seats. However, if you’re looking for a break from the suspense, you can dive into the latest developments in tower of god chapter 597 . This chapter delves deeper into the complexities of the Tower and its enigmatic characters.
Once you’ve caught up on the Tower’s latest events, return to unique fabricating chapter 7 and witness the thrilling conclusion of this extraordinary saga.
Material Selection Criteria
The selection of materials for Chapter 7 fabrications is guided by several key criteria:
- Electrical Conductivity: The material must possess high electrical conductivity to facilitate efficient current flow and minimize resistive losses.
- Thermal Stability: The material must be able to withstand high temperatures during fabrication processes and maintain its properties under operating conditions.
- Mechanical Strength: The material must be mechanically strong to withstand the stresses encountered during fabrication and device operation.
- Chemical Inertness: The material must be chemically inert to prevent degradation or contamination during fabrication and device operation.
Comparative Analysis of Material Options
Various materials can be considered for Chapter 7 fabrications, each with its unique properties and advantages. A comparative analysis of different material options is essential to determine the most suitable choice for specific applications.
The unique fabricating Chapter 7 is a testament to the author’s imagination, weaving a tapestry of intricate characters and plotlines. If you’re seeking an equally captivating read, dive into Black Clover Chapter 353 , where epic battles and heartwarming moments collide.
Returning to our initial topic, Unique Fabricating Chapter 7, it’s clear that the author’s prowess shines through every page, leaving readers eagerly anticipating the next chapter.
Material | Electrical Conductivity | Thermal Stability | Mechanical Strength | Chemical Inertness |
---|---|---|---|---|
Copper | High | Moderate | Moderate | Low |
Gold | High | High | Low | High |
Aluminum | High | Moderate | Low | Moderate |
Nickel | Moderate | High | High | Moderate |
Titanium | Moderate | High | High | High |
Design Considerations
Fabrications for Chapter 7 bankruptcy present unique design considerations due to the need for efficiency, cost-effectiveness, and compliance with legal requirements. These considerations significantly influence the design process, requiring innovative approaches to achieve optimal outcomes.
Factors Influencing the Design Process
- Complexity of the Bankruptcy Case: The severity of the financial distress and the number of creditors involved can affect the complexity of the design.
- Type of Bankruptcy Filing: The specific type of bankruptcy filing, such as Chapter 7 liquidation or Chapter 11 reorganization, influences the design approach.
- Legal Regulations: Bankruptcy laws and regulations impose specific requirements that must be met in the design of the fabrication.
- Cost Constraints: Fabrications must be designed to minimize costs while still meeting legal and operational requirements.
Quality Control and Testing: Unique Fabricating Chapter 7
Ensuring the quality of fabricated products is crucial in Chapter 7. To achieve this, unique quality control measures and testing procedures are implemented to guarantee product integrity and adherence to industry standards.
Unique Quality Control Measures
- Non-Destructive Testing (NDT): Advanced NDT techniques, such as ultrasonic testing and radiography, are employed to detect defects and flaws without damaging the product.
- In-Process Inspection: Regular inspections are conducted throughout the fabrication process to identify potential issues and ensure compliance with design specifications.
- Statistical Process Control (SPC): SPC techniques are used to monitor and control critical process parameters, reducing the likelihood of defects.
Testing Procedures
Rigorous testing procedures are conducted to verify product performance and meet industry standards:
- Mechanical Testing: Tensile, compression, and fatigue tests assess the material’s strength, ductility, and durability.
- Environmental Testing: Products are exposed to extreme temperatures, humidity, and other environmental conditions to ensure they meet specifications.
- Functional Testing: Products are tested under actual operating conditions to verify their performance and reliability.
Standards and Specifications
All fabricated products must meet stringent standards and specifications:
- ASTM International Standards: Products adhere to globally recognized ASTM standards for material properties, testing methods, and quality control.
- ISO Certification: Fabrication processes are certified to ISO standards, ensuring adherence to international quality management systems.
- Customer-Specific Specifications: Products meet the specific requirements and tolerances defined by individual customers.
Closing Notes
In the realm of Chapter 7 fabrications, we’ve navigated the intricacies of unique fabricating methods, material properties, design considerations, quality control, and testing. This exploration has illuminated the distinctive characteristics that set Chapter 7 apart, empowering us with a deeper understanding of the art and science behind these exceptional fabrications.
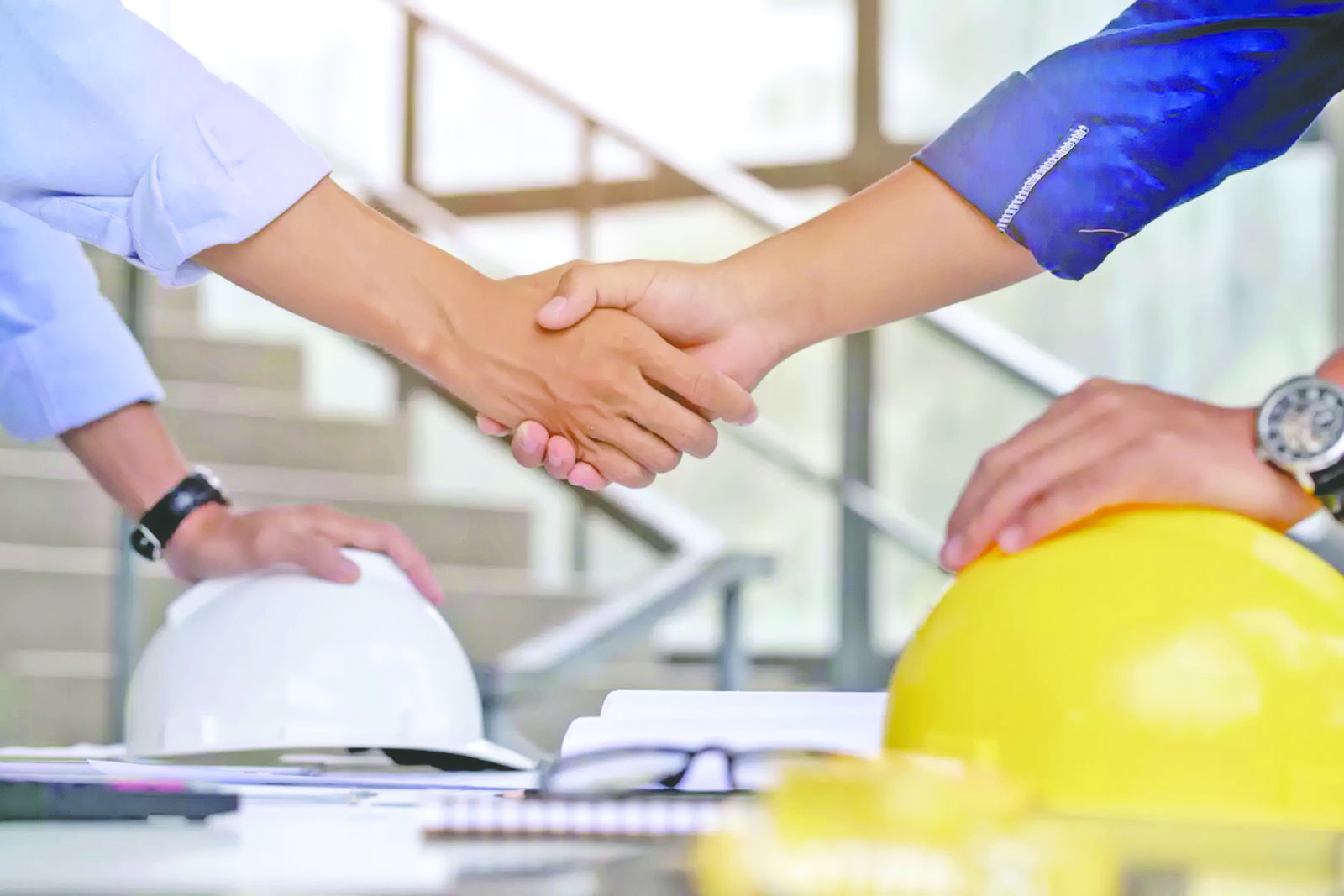